Evolution of pipeline leak detection
Leak detection requirements around the world
Buried underground, the pipeline system tends to get less attention than other infrastructure systems like highways and bridges. In addition, regulatory oversight of pipeline safety, operations, and worthiness is somewhat fragmented based on what is being transported. Key examples include crude oil pipelines from oil fields to refineries; multiproduct pipelines from refineries to tank farms; subsea pipelines from floating production storage and offloading (FPSO) units and platforms; non-continuously operated transport pipelines (for example, for jet fuel); water pipelines from desalination plants to cities; and natural gas pipelines.
Leak detection awareness has grown in recent years, spurred by hundreds of incidents – small and large. Explosions caused by pipeline leaks have killed or injured hundreds, while millions of gallons have leaked from heavy crude oil pipelines onto land or into the ocean.
Recognising the importance of leak detection, the US Department of Transportation (DOT), Pipeline and Hazardous Materials Safety Administration (PHMSA), Office of Pipeline Safety (OPS) has included leak detection provisions and considerations in numerous individual federal regulatory guidelines.
In addition, a federal leak detection study, prepared in response to the Pipeline Safety, Regulatory Certainty, and Job Creation Act of 2011, sets the tone for a broader national conversation. The 2012 study1 notes, “Due to the vast mileage of pipelines throughout the nation, it is important that dependable leak detection systems are used to promptly identify when a leak has occurred so that appropriate response actions are initiated quickly. The swiftness of these actions can help reduce the consequences of accidents or incidents to the public, environment, and property.”
The landmark study looked at leak detection systems used by operators of hazardous liquid pipeline facilities and transportation-related flow lines. It analysed the technical limitations of current leak detection systems, suggested what might be done to encourage development of better technologies, and analysed practical leak detection standards.
Other important regulatory background includes the German Technical Rule for Pipelines (TRFL), which contains the most stringent pipeline leak detection requirements in the world. TRFL requires pipeline operators to install a leak detection system that uses two continuously operating technical processes based on different physical variables that can detect leaks in the steady state. They require a system or process for detecting leaks during transient operating conditions; a system or process that can detect leaks during standstill conditions; a system or process that detects gradual leaks; and a system or process for leak localisation. In summary, these rules require leak detection systems to cover all kind of daily pipeline operation, with no exclusions.
Pipeline leak detection systems
There are three basic leak detection systems: internal, external, and visual inspection.1
Internal systems use measurement sensors providing flow or pressure readings, and perform calculations to estimate the state of the fluids within the pipe. These systems must follow recommended practices found in American Petroleum Institute (API) 1130 Computational Pipeline Monitoring for Liquid Pipelines. The three main categories of internal systems include:
- Regular or periodic monitoring of operational data by controllers, using such methods as volume balance; pressure/flow monitoring; pressure point analysis; and the negative pressure wave method.
- Computational pipeline monitoring (CPM), using mass balance with line pack correction; real time transient modelling (RTTM); statistical pattern recognition; pressure/flow pattern recognition; and negative pressure wave modelling/signature recognition.
- Data analysis methods, including statistical methods and digital signal analysis.
External systems use dedicated instrumentation equipment and sensors, typically located externally to the pipe, to detect escaped fluids. Unlike internal systems, there are no accepted API engineering standards for engineers designing external systems, making careful deployment and installation critical. A misplaced sensor could easily miss an escaping hydrocarbon plume.
Available external sensor systems include:
- Acoustic sensors
- Hydrocarbon sensing fibre optics
- Temperature sensing cables
- Liquid sensing cables
- Vapour sensing tubes
- Chemical vapor sensors
- Optical methods
Visual inspection systems include examining the pipeline from the outside to determine if there is a leak. This can be done by flying over with a drone or helicopter, driving alongside the pipeline, or using fibre optics on the full pipeline length to detect temperature changes. Because it relies on human intervention, visual inspection is considered the most effective of all methods – but it is extremely expensive. Requirements and standards for inspection systems are covered by API 570: Piping Inspection Code: In-service Inspection, Rating, Repair, and Alteration of Piping Systems.
Table 1 provides a general comparison among the systems for a variety of parameters. However, it should be noted that the Leak Detection Study notes that it is good engineering practice to use separate subsystems, including internal, external, and inspection technologies. “They should be carefully selected and engineered to complement each other,” the study states.
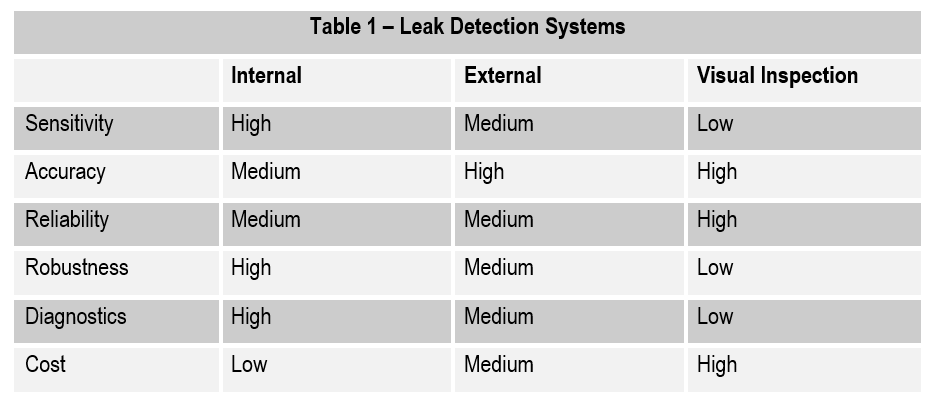
New extended real time transient model-based leak detection and localisation technology
In recent years, new extended real time transient model (E-RTTM) computational pipeline monitoring technology has been developed into PipePatrol, a detection system that can be used for monitoring and protection of pipelines in all operating conditions – from a long or short distance pipeline for oil, gas, or water, to refined products in the chemical industry or others.
The system meets API 1130, API 1175, California AB 864, and German TRFL standards, as well as CSA Z662 Oil & Gas Pipeline Systems standards. The system also complies with numerous global company standards, including Shell DEP 31.40.60.11-Gen., Kuwait Oil Company Recommended Practice KOC-MP-039, DOW Global LDS Standard, and Saudi Aramco SAES SAES-Z003.
Using a unique leak pattern recognition algorithm, the E-RTTM technology allows extremely fast and sensitive leak detection in any kind of pipeline operation – without generating false alarms. Unlike other systems, it does not simply compare outlet flow with inlet flow. Instead, it uses the measured conditions to calculate the hydraulic profiles of the pipeline. One of these, the calculated flow profile, is compared to the measured flow for both inlet and outlet to determine what the pipeline flow should be if there is no leak.
In the first stage of E-RTTM, to generate the specific leak patterns, a fully dynamic, real-time process model calculates target values. This model is based on the method of characteristics considered the most accurate for 1-dimensional flows in pipelines. It has been continuously improved over the last few years, and now includes a full thermal/temperature model, so it can accurately model crude oil or dense phase gases like supercritical CO2 or ethylene.
Information about the real pipeline is transferred into a computer, including the elevation profile, product and material characteristics, and the thermodynamic equation.
Based on the physical laws of conservation of momentum, mass and energy, a virtual pipeline is developed, driven by the online measurements. This virtual pipeline now calculates what the pipeline flow should be if there is no leak.
As deviations will be created by other events, decision values are processed by the second stage, signature analysis. Signature analysis continuously monitors decision values for different kinds of patterns. Depending on the detected pattern, the system will suppress a message, raise a warning, or raise a leak alarm. Therefore, not every deviation will lead to an alarm, which avoids false alarming. This is key, because false alarms can be extremely expensive when they shut down the line or process or lead to flaring of the product.
In summary, unlike other CPM methods, E-RTTM does not simply compare outlet flow with inlet flow. Instead, it uses the measured conditions to calculate the hydraulic profiles of the pipeline. One of these, the calculated flow profile, is compared to the measured flow for both inlet and outlet.
The signature analysis method uses leak pattern recognition to continuously analyse this data and determine the pipeline’s leak status. Because E-RTTM uses relative values, it continues to work effectively under transient pipeline conditions, without any significant effect on its sensitivity.
In addition to leak detection, the system includes a variety of modules that provide other important operational benefits. These include theft detection, tightness monitoring, predictive modelling, line break detection, stress monitoring, and batch tracking, as well as pump monitoring, data acquisition and cyber security.
In fact, the PipePatrol system was cited in the PHMSA Leak Detection Study, which noted, “There is no reason why several different internal leak detection methods should not be implemented at the same time. In fact, a basic engineering robustness principle calls for at least two methods that rely on entirely separate physical principles. As an example, the Extended-RTTM system trademarked by KROHNE Industries, USA uses an RTTM in conjunction with several other API 1130 techniques.”
Pipeline operators use E-RTTM system to reduce resources while increasing reliability
Pipeline operators are turning to the E-RTTM-based system to meet existing and new leak detection regulatory requirements. These include a very wide range of products, for example, gas (including non-ideal sub-critical and supercritical/dense phase gases), single product liquids, crude oil, multi-product liquids (including refined products), liquefied petroleum gas (LPG), liquefied natural gas (LNG), brine, water and wastewater.
One example is a chemical facility in South Charleston, West Virginia, where the PipePatrol E-RTTM system is being used in a 7-mile 4-inch ethylene oxide pipeline.
Another example is a plant in Freeport, Texas, which is using the system, including rupture detection, on a 12-inch liquified ethane gas line to meet new API RP 1175 requirements for a rupture alarm independent from the leak alarm. The operators integrated the new alarm into the PipePatrol system by adding another leak pattern with a dedicated alarm.
A final example is a partnership with NuGen, in which the PipePatrol system was used by a California-based company for the Torrance Refinery pipeline network, which transports crude oil and refined products. The network includes more than 18 pipelines, from crude oil gathering lines over transport pipelines, to refinery and all connecting lines, to airport, truck loading and unloading and partner companies. The system, which can monitor everything from 400-feet lines to a 400-mile line, also includes API 1175 rupture detection.
Smart monitoring and protection of pipelines
Pipeline monitoring has evolved from simple mass balance approaches to entire systems that can offer leak, theft and line break detection, as well as monitoring of tightness and lifetime stress. Covering operational, security, environmental, and legislative requirements, the new systems provide complete and sensitive protection of oil, gas, water and multiproduct pipelines.
References:
- US Department of Transportation Pipeline and Hazardous Materials Safety Administration Final Report No. 12-173 Final Report Leak Detection Study – DTPH56-11-D-000001, Kiefner and Associates, Inc. By Dr. David Shaw, Dr. Martin Phillips, Ron Baker, Eduardo Munoz, Hamood Rehman, Carol Gibson, Christine Mayernik, December 10, 2012.
For more information:
This article was written by Joe Incontri, KROHNE Inc.